Chemical oxidation method is a traditional method for preparing expandable graphite. In this method, natural flake graphite is mixed with appropriate oxidant and intercalating agent, controlled at a certain temperature, constantly stirred, and washed, filtered and dried to obtain expandable graphite. Chemical oxidation method has become a relatively mature method in industry with the advantages of simple equipment, convenient operation and low cost.
The process steps of chemical oxidation include oxidation and intercalation.The oxidation of graphite is the basic condition for the formation of expandable graphite, because whether the intercalation reaction can proceed smoothly depends on the degree of opening between the graphite layers.And natural graphite at room temperature has excellent stability and acid and alkali resistance, so it does not react with acid and alkali, therefore, the addition of oxidant has become a necessary key component in chemical oxidation.
There are many kinds of oxidants, generally used oxidants are solid oxidants (such as potassium permanganate, potassium dichromate, chromium trioxide, potassium chlorate, etc.), can also be some oxidizing liquid oxidants (such as hydrogen peroxide, nitric acid, etc.). It is found in recent years that potassium permanganate is the main oxidant used in preparing expandable graphite.
Under the action of oxidizer, graphite is oxidized and the neutral network macromolecules in the graphite layer become planar macromolecules with positive charge. Due to the repulsive effect of the same positive charge, the distance between the graphite layers increases, which provides a channel and space for the intercalator to enter the graphite layer smoothly. In the preparation process of expandable graphite, the intercalating agent is mainly acid. In recent years, researchers mainly use sulfuric acid, nitric acid, phosphoric acid, perchloric acid, mixed acid and glacial acetic acid.
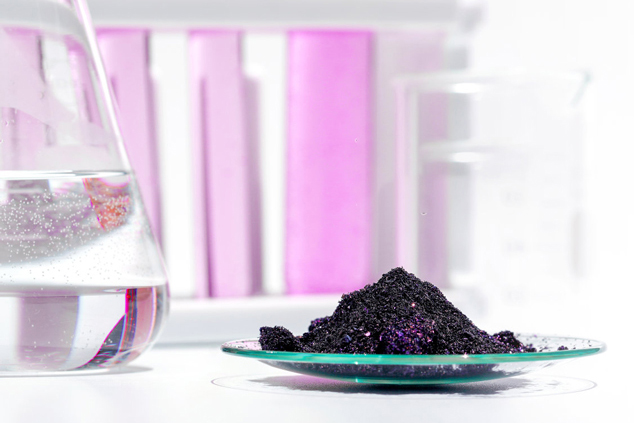
Electrochemical method is in a constant current, with the aqueous solution of the insert as the electrolyte, graphite and metal materials (stainless steel material, platinum plate, lead plate, titanium plate, etc.) constitute a composite anode, metal materials inserted in the electrolyte as cathode, forming a closed loop; Or the graphite suspended in the electrolyte, in the electrolyte at the same time inserted in the negative and positive plate, through the two electrodes are energized method, anodic oxidation. The surface of graphite is oxidized to carbocation. At the same time, under the combined action of electrostatic attraction and concentration difference diffusion, acid ions or other polar intercalant ions are embedded between the graphite layers to form expandable graphite.
Compared with the chemical oxidation method, the electrochemical method for the preparation of expansable graphite in the whole process without the use of oxidant, the treatment amount is large, the residual amount of corrosive substances is small, the electrolyte can be recycled after the reaction, the amount of acid is reduced, the cost is saved, the environmental pollution is reduced, the damage to the equipment is low, and the service life is extended.In recent years, electrochemical method has gradually become the preferred method for preparing expandable graphite by many enterprises with many advantages.
The gas-phase diffusion method is to produce expandable graphite by contacting the intercalator with graphite in gaseous form and intercalating reaction.Generally, the graphite and the insert are placed at both ends of the heat-resistant glass reactor, and the vacuum is pumped and sealed, so it is also known as the two-chamber method.This method is often used to synthesize halide -EG and alkali metal -EG in industry.
Advantages: the structure and order of the reactor can be controlled, and the reactants and products can be easily separated.
Disadvantages: the reaction device is more complex, the operation is more difficult, so the output is limited, and the reaction to be carried out under high temperature conditions, the time is longer, and the reaction conditions are very high, the preparation environment must be vacuum, so the production cost is relatively high, not suitable for large-scale production applications.
The mixed liquid phase method is to directly mix the inserted material with graphite, under the protection of the mobility of inert gas or sealing system for heating reaction to prepare expandable graphite. It is commonly used for the synthesis of alkali metal-graphite interlaminar compounds (GICs).
Advantages: The reaction process is simple, the reaction speed is fast, by changing the ratio of graphite raw materials and inserts can reach a certain structure and composition of expandable graphite, more suitable for mass production.
Disadvantages: The formed product is unstable, it is difficult to deal with the free inserted substance attached to the surface of GICs, and it is difficult to ensure the consistency of graphite interlamellar compounds when a large number of synthesis.
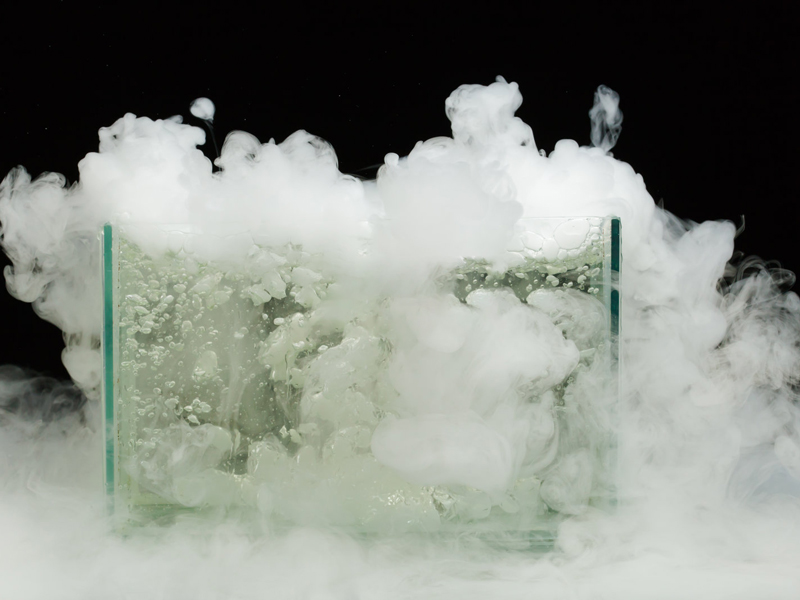
The melting method is to mix graphite with intercalating material and heat to prepare expandable graphite.Based on the fact that eutectic components can lower the melting point of the system (below the melting point of each component), it is a method for the preparation of ternary or multicomponent GICs by inserting two or more substances (which must be able to form a molten salt system) between graphite layers simultaneously.Generally used in the preparation of metal chlorides - GICs.
Advantages: The synthesis product has good stability, easy to wash, simple reaction device, low reaction temperature, short time, suitable for large-scale production.
Disadvantages: it is difficult to control the order structure and composition of the product in the reaction process, and it is difficult to ensure the consistency of the order structure and composition of the product in mass synthesis.
The pressurized method is to mix graphite matrix with alkaline earth metal and rare earth metal powder and react to produce M-GICS under pressurized conditions.
Disadvantages: Only when the vapor pressure of the metal exceeds a certain threshold, the insertion reaction can be carried out; However, the temperature is too high, easy to cause metal and graphite to form carbides, negative reaction, so the reaction temperature must be regulated in a certain range.The insertion temperature of rare earth metals is very high, so pressure must be applied to reduce the reaction temperature.This method is suitable for the preparation of metal-GICS with low melting point, but the device is complicated and the operation requirements are strict, so it is rarely used now.
Explosive method generally uses graphite and expansion agent such as KClO4, Mg(ClO4)2·nH2O, Zn(NO3)2·nH2O pyropyros or mixtures prepared, when it is heated, graphite will simultaneously oxidation and intercalation reaction cambium compound, which is then expanded in an "explosive" way, thus getting expanded graphite.When metal salt is used as expansion agent, the product is more complex, which not only has expanded graphite, but also metal.
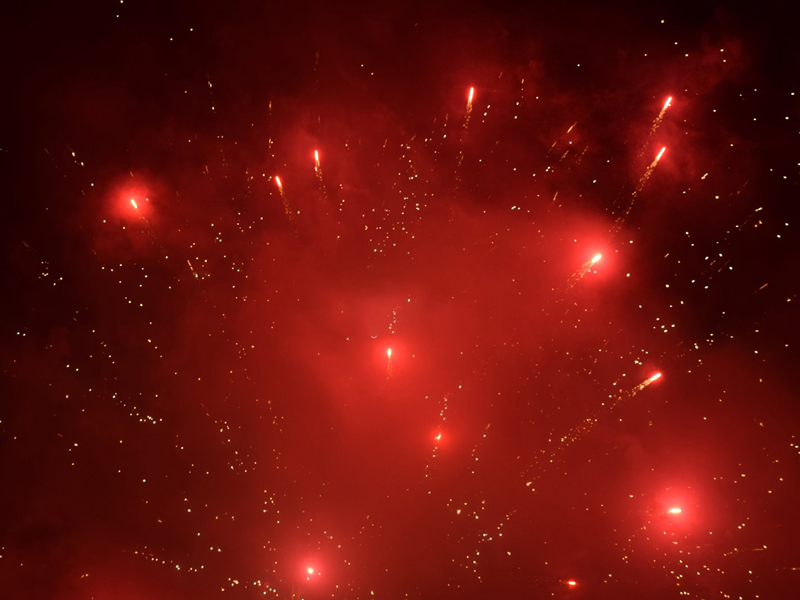